Aluminium versus stainless steel machining
Key differences in CNC parameters
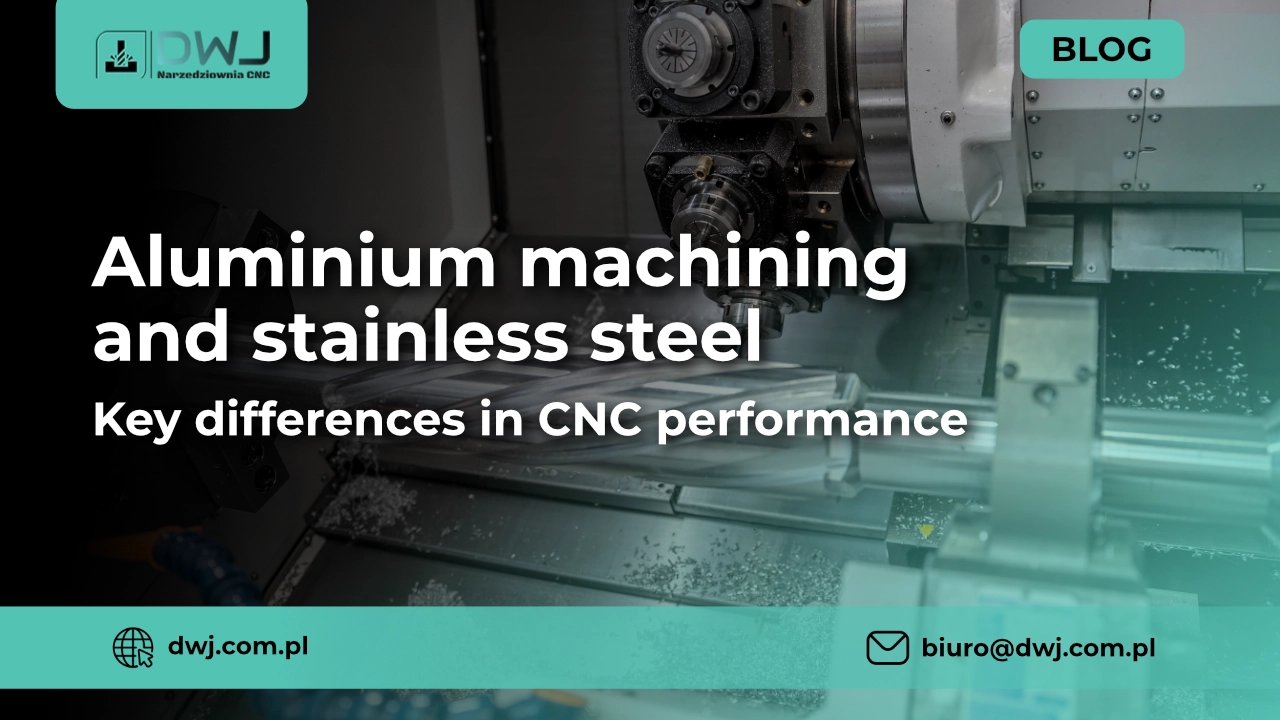
Choosing the right material for the production of CNC parts has a huge impact on the efficiency of the process, cost and quality of the final product. The two most common material groups in CNC machining are aluminium and stainless steel. Although both metals are widely used in industry, their machining requires completely different cutting parameters, tools and strategies. In this article, we will compare aluminium machining and stainless steel machining, discussing the key differences, challenges and optimal CNC machine settings.
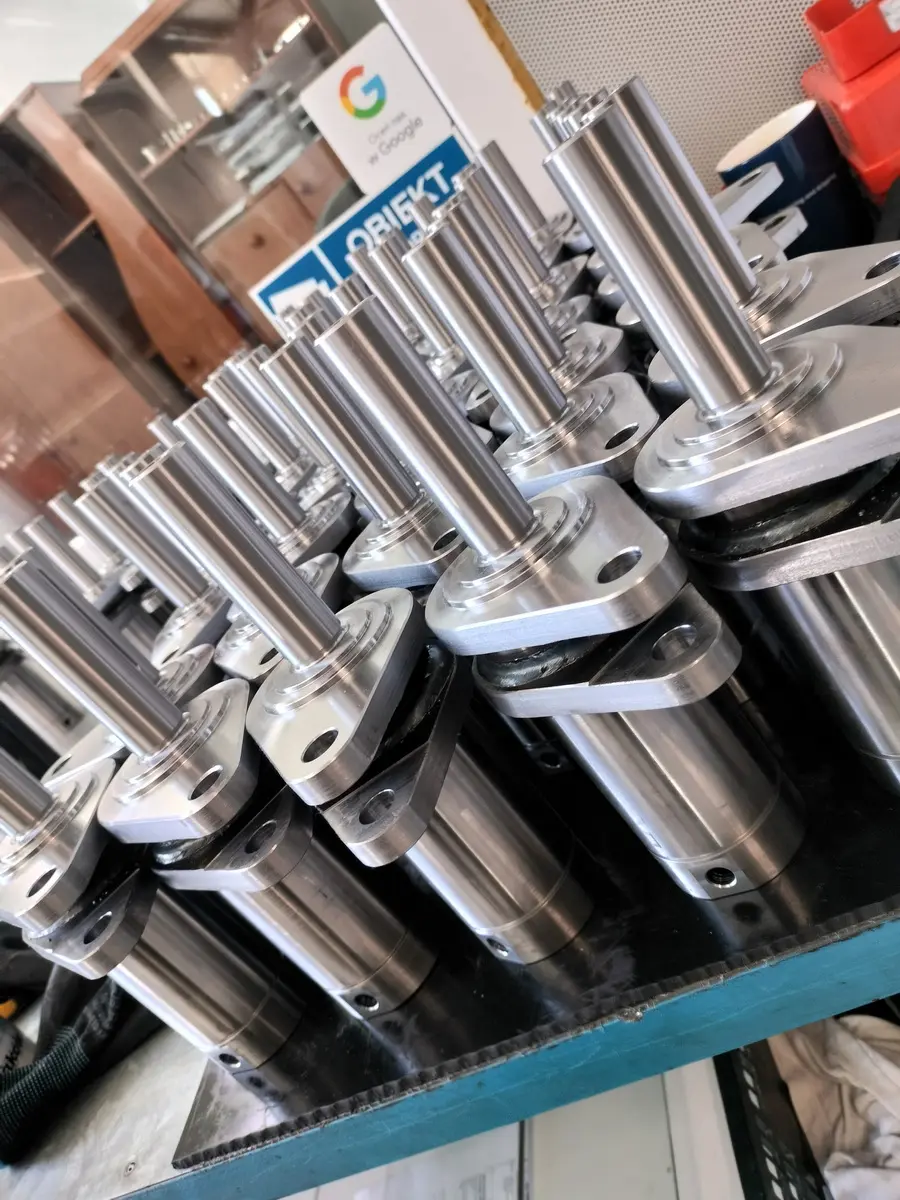
Material properties and CNC machining
Aluminium – lightweight and easy to process
Aluminium is one of the most commonly machined metals in CNC due to:
– Low density (approx. 2.7 g/cm³) – easy to machine at high speeds
– Good thermal conductivity – less risk of tool overheating
– Softness – less stress on cutting tools
However, aluminium also has disadvantages:
– Tendency to stick to tools (carbon build-up)
– Requires sharp tools to avoid jagged edges
Stainless steel – tough but demanding
Stainless steel (e.g. 304, 316) is much more difficult to machine due to:
- High hardness and strength – higher tool loading
- Low thermal conductivity – rapid heating of blades
- High toughness – tendency to form a long chip that can wrap around the cutter
Differences in CNC machining parameters
The key to effective CNC machining is to precisely adjust the machine parameters to the characteristics of the material being machined. Aluminium and stainless steel require radically different settings for cutting speed, feed rate and depth of cut. In this section, we will compare the optimum parameters for both materials in detail, explaining why aluminium allows faster machining, while stainless steel requires a more careful approach. You will learn specific values and formulas that will help you avoid common mistakes when programming CNC machines.
Cutting speed (Vc)
- Aluminium machining:
Recommended speeds are 200-500 m/min (for milling) and 150-300 m/min (for turning).
High speeds are possible due to the good thermal conductivity of aluminium. - Stainless steel machining:
Much lower speeds – 50-120 m/min (milling) and 80-150 m/min (turning).
Too high a speed leads to rapid tool wear.
Speed (n)
Example for a cutter with a diameter of 10 mm:
- Aluminium:
At Vc = 300 m/min → ~9550 rpm - Stainless steel:
At Vc = 80 m/min → ~2550 rpm
Feed rate (f)
- Aluminium: High feed rate (0.1-0.3 mm/rev) – fast material removal
- Stainless steel: Low feed rate (0.05-0.15 mm/rev) – avoids excessive loads
Depth of cut (ap)
- Aluminium: Large depth (up to 1× tool diameter)
- Stainless steel: shallower cutting (0.2-0.5× tool diameter)
Why does aluminium allow faster processing than stainless steel?
Aluminium is one of the easiest metals to machine, which translates into significantly higher productivity in CNC processes compared to stainless steel. The key factors determining this difference are:
1. Lower hardness and strength
- Aluminium (typically 15-120 HB) is 3-4 times softer than typical stainless steels (150-300 HB)
- Lower cutting resistance = lower tool loading
- Possibility of using more aggressive parameters (greater depths of cut and feed rates)
2. Excellent thermal conductivity
- Aluminium: ~200 W/(m-K) vs stainless steel: ~15 W/(m-K)
- Rapid heat removal from the cutting zone
- Reduced risk of tool overheating and thermal distortion
3. Improved chip breakage
- Aluminium forms short, brittle chips
- Stainless steel generates long, ductile chips (drainage problem)
- In the case of aluminium, less risk of swarf wrapping around the tool
4. Higher permissible cutting speeds
- Typical Vc for aluminium: 200-500 m/min
- Typical Vc for steel: 50-120 m/min
- The difference is due to:
- Less viscous aluminium
- Improved resistance to abrasive wear
5. Less tool wear
- Cutters for aluminium stay sharp 3-5 times longer than those for steel
- Lower tool operating costs
Practical effect: machining time in aluminium can be 2-4 times shorter than in stainless steel for similar workpiece geometries. For example, pocket milling in aluminium often takes 30 minutes, while the same operation in steel takes 1.5-2 hours.
Exceptions: some aluminium alloys (e.g. 2000 series with copper) may require slower machining due to increased hardness.
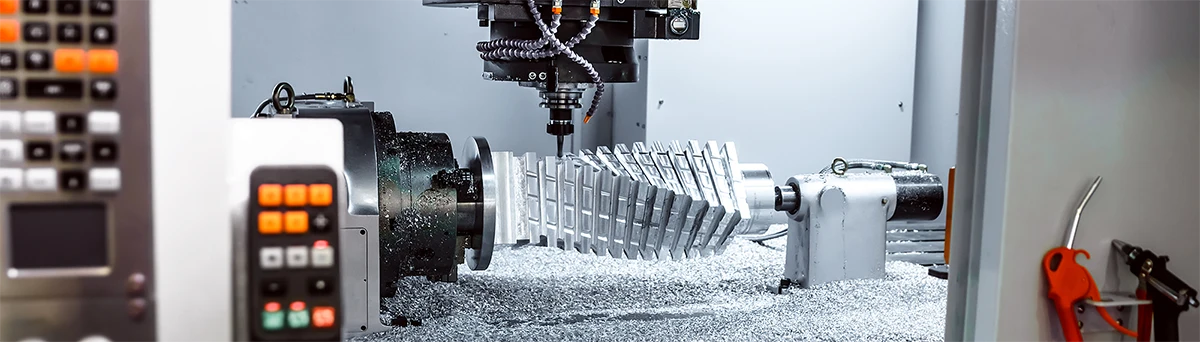
Selection of tools for machining aluminium and steel
Selecting the right tools is one of the most important factors in determining the effectiveness of CNC machining. Aluminium and stainless steel have completely different cutting properties and therefore require specially designed cutters, drills and lathe knives. In this section, we discuss which tools work best for machining each of these materials, taking into account their geometry, coatings and working conditions.
Cutters for aluminium
- Tool material: Carbide (WC) with TiB2 or diamond coating (PCD).
- Geometry: Sharp edges, large chip space
- Number of blades: 2-3 (for better chip evacuation)
Cutters for stainless steel
Tool material: Carbide with TiAlN or AlCrN coating
- Geometry: Robust design, smaller rake angle
- Number of blades: 4-6 (for better stability)
Cooling and lubrication
- Aluminium machining:
Recommended liquid (emulsion) or air cooling – prevents material sticking - Stainless steel machining:
High pressure cooling (HPC) required – reduces heat build-up
Bottom line – which treatment is more expensive?
- Machining aluminium is faster and cheaper due to high speeds and less tool wear.
- Machining stainless steel requires slower parameters, more expensive tools and longer machining times, which increases costs.
If you need professional aluminium machining or stainless steel machining, contact us – we will select the optimal CNC parameters for your project!