How to select the optimum CNC machining parameters? Practical Guide
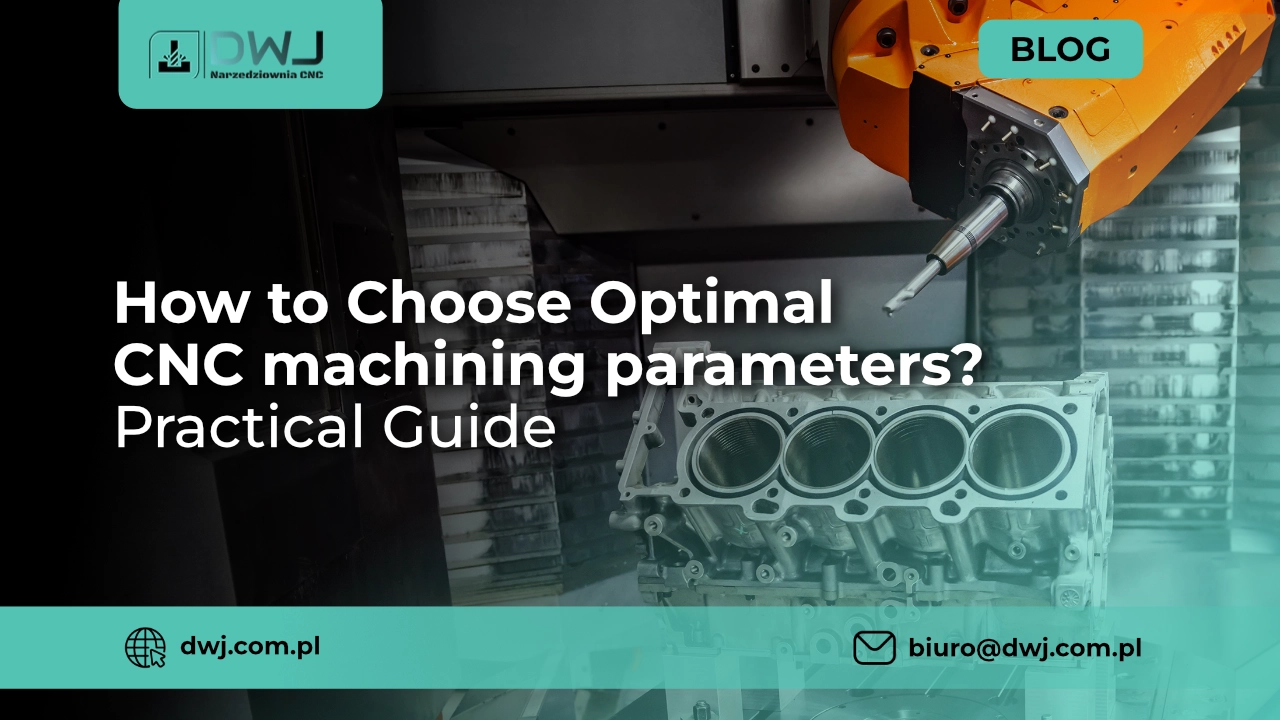
CNC machining is a process that requires precision, knowledge and experience. One of the key factors determining the quality and efficiency of this process is the selection of optimal machining parameters. Incorrect settings can lead to damage to tools, the material being machined and even the machine. In this article, we will provide a practical guide on how to choose the best CNC machining parameters to achieve excellent results.
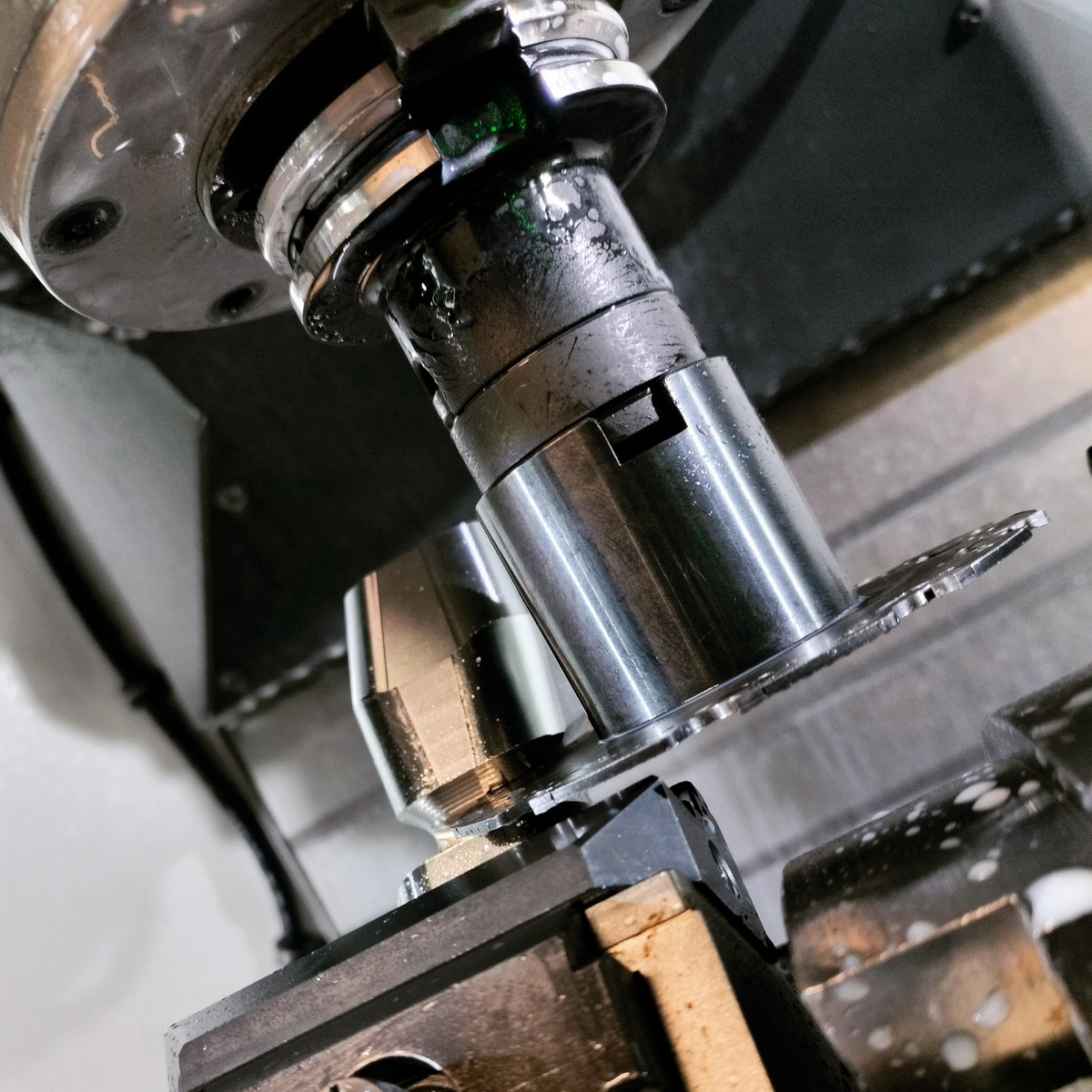
Understanding the Basic Parameters of CNC Machining
Before going into detail, it is worth knowing the basic parameters that affect the CNC machining process:
Cutting speed (Vc): The speed at which the cutting edge of the tool moves relative to the material. It is measured in metres per minute (m/min).
Rotational speed (n): The number of spindle revolutions per minute (rpm). Depends on the cutting speed and tool diameter.
Feed rate (f): The speed at which the tool moves relative to the workpiece. It is measured in millimetres per revolution (mm/rev) or millimetres per minute (mm/min).
Depth of cut (ap): The depth to which the tool enters the material in one pass. It is measured in millimetres (mm).
Cutting speed selection (Vc)
Cutting speed is one of the most important parameters, as it affects tool life, surface quality and process efficiency. Too high a speed can lead to overheating of the tool and too low a speed can lead to inefficient machining.
How do you select the cutting speed?
-
Workpiece material: Each material has a recommended cutting speed by the manufacturer of the cutting inserts we use. Each tool manufacturer specifies a minimum, maximum and output speed for the tool. It is worth looking at the insert packaging or tool catalogue.
-
Tool type: The main tools used are carbide inserts and cutters, ceramic, CBN. In the past, HSS was often used where cutting speeds were low.
-
Machining conditions: Cooling, clamping stability, machine and type of machining (e.g. roughing or finishing) also affect speed selection.
Selection of the rotational speed (n)
The speed is directly related to the cutting speed and tool diameter. It can be calculated using the formula:
n=Vc×1000π×Dn=π×DVc×1000
where:
- nn – rotational speed (rpm),
- Vc – cutting speed (m/min),
- DD – tool diameter (mm).
Example:
If the cutting speed is 250 m/min and the cutter diameter is 10 mm, the speed will be:
n=250×10003.14×10≈7962 obr/minn=3.14×10250×1000≈7962obr/min
Determining the feed rate (f)
The feed rate determines how fast the tool moves relative to the material. A feed rate that is too high can lead to tool damage, while a feed rate that is too low can lead to longer machining times and faster cutting edge wear.
How do I choose my feed rate?
- Too low: this can lead to faster blunting of the tool, can create build-up and is less economical. Mainly used for finishing.
- Too high: can lead to chipping of the cutting edge, high surface roughness and deformation of the material can occur.
Depth of cut (ap)
In turning, ap determines the radial thickness of the layer of material removed in one pass of the turning knife.
- Coarse turning (large volume of material to be cut)
ap = 1-10 mm (sometimes more for rigid machines), greater depth allows faster material removal but requires a strong machine tool, used when machining raw castings, shafts, tubes.
- Finishing (fine machining, improved surface quality)
ap = 0.05-2 mm, shallow depth to achieve a smooth surface, requires sharp tools and low feed rate.
Factors affecting ap in lupus:
Workpiece material – for steel ap ≈ 2-6 mm, for aluminium higher values can be used. Stiffness of lathe system – vibration limits maximum ap. Type of lathe knife – knives with carbide inserts allow higher ap.
In milling, ap refers to the height difference between the work surface and the lowest cutting point of the cutter.
How do you select ap in milling?
-
Coarse milling (rapid material removal)
ap = 2-10 mm (depending on the rigidity of the machine tool), greater depths can be used for face milling and large cutters.
- Finishing milling (fine machining, improved surface quality)
ap = 0.1-2 mm, the shallow depth ensures high dimensional accuracy.
Factors influencing ap in milling
- Type of cutter – larger cutter diameters allow greater ap.
- Spindle and toolholder rigidity – limits maximum depth of cut.
- Type of milling – face milling → larger ap, circumferential milling→ ap depends on milling cutter width.
- Machine tool power – larger ap requires a more powerful spindle.
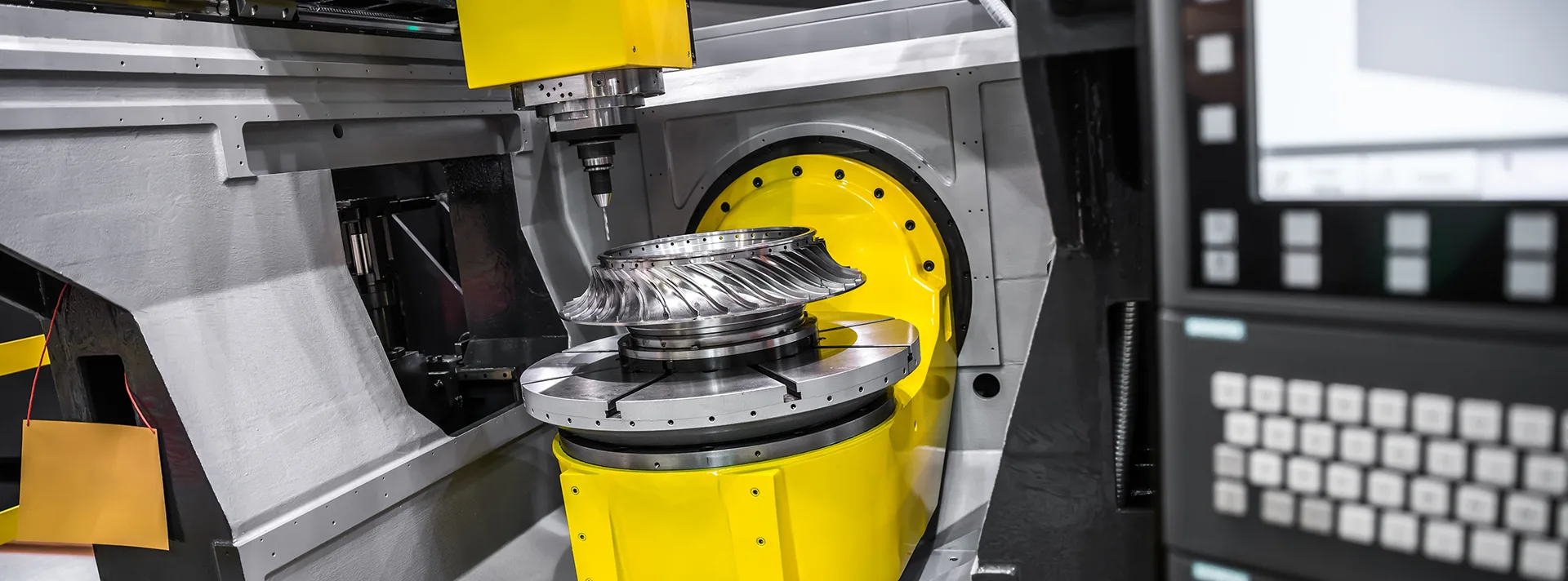
Consideration of Cooling and Lubrication
Adequate cooling and lubrication are key to extending tool life and improving machining quality. Depending on the material and type of machining, the following can be used:
- Liquid cooling:
– Turning and milling of steel, aluminium and cast iron alloys.
– Machining requiring high cutting speeds and precision.
– Deep drilling, where chip evacuation is crucial.
- Air cooling:
– Machining of aluminium, magnesium alloys and composites.
– Operations where the coolant could contaminate the material or cause thermal shock to the cutting edge.
– Milling of thin-walled components where coolant could cause distortion.
- Dry processing:
– Hard turning with ceramic or CBN tools.
– Coolant-sensitive materials (e.g. some composites).
– Dry machining in the aerospace and automotive industries.
Testing and optimisation
The selection of CNC machining parameters is an iterative process. It is recommended that:
- Testing on samples: Test various parameters on small fragments of material or on a sample batch.
- Process monitoring: Observe tool wear, surface quality and machining time.
- Parameter correction: Adjust parameters based on test results.
Summary
Choosing the optimum CNC machining parameters is the key to efficient and precise production. Remember that every material, tool and project requires an individual approach. Using the tips above, you can significantly improve machining quality, extend tool life and increase process efficiency. If in doubt, it is always advisable to consult an experienced CNC operator or engineer.