Metalworking services at DWJ
Hardening, nitriding, anodising and blackening
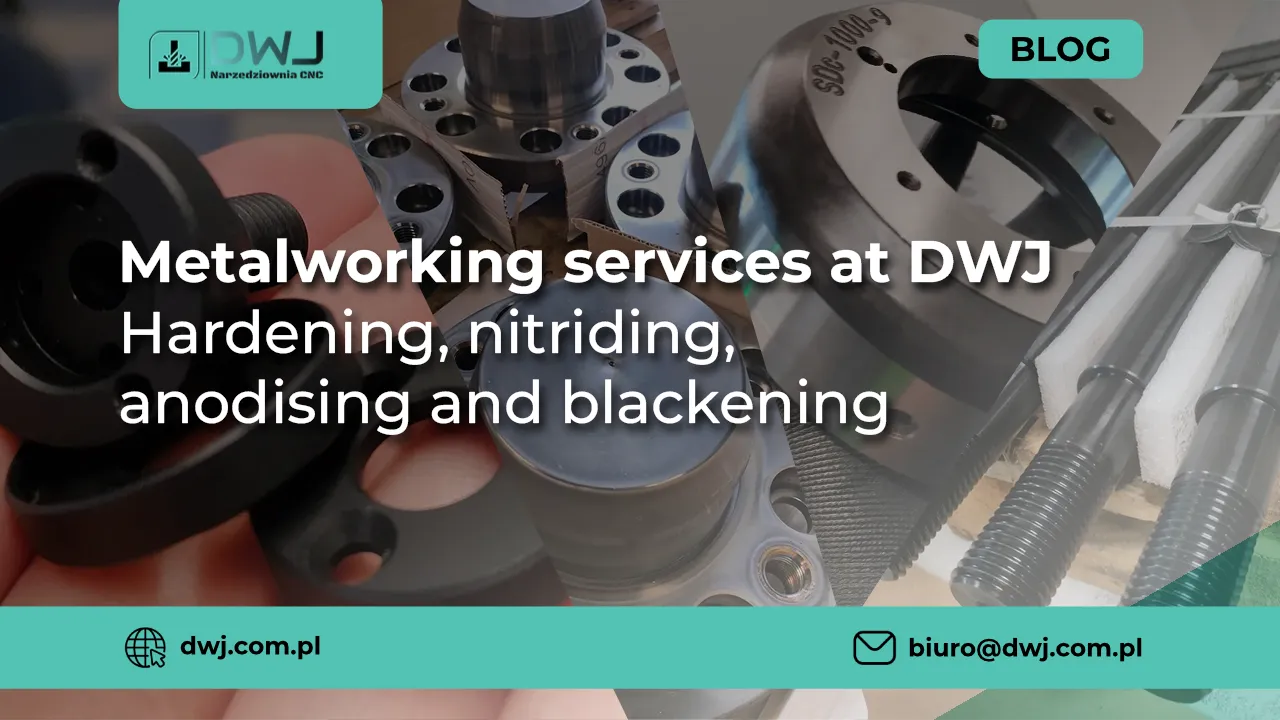
Metalworking is a key process in many industries, allowing metal components to have the desired physical, chemical and aesthetic properties. DWJ Narzędziownia offers comprehensive services in the field of specialised thermo-chemical and surface treatment of metals, including hardening, nitriding, anodising and blackening. Thanks to modern technologies and many years of experience, DWJ ensures the highest quality of the processes carried out, tailored to individual customer needs.
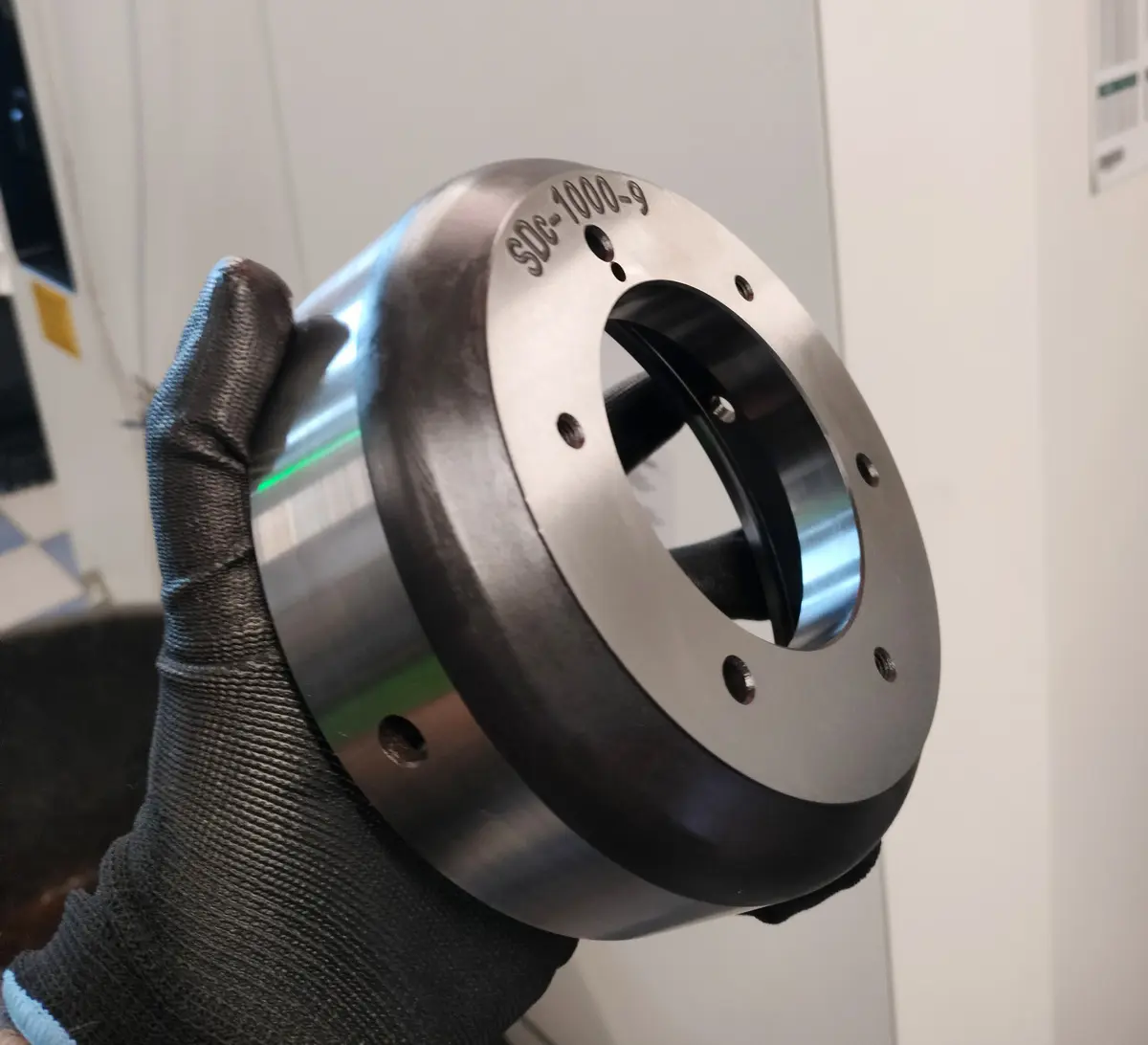
Hardening – Increasing Strength and Hardness
Hardening is one of the fundamental heat treatment processes of steel, necessary to achieve the desired performance properties. Its overriding objective is to significantly increase the hardness of the material, which directly affects its tensile strength and key wear resistance.
The technological process itself involves carefully heating the steel to an appropriate, well-defined temperature, known as the austenitising temperature, at which the structural transformation to austenite takes place. The component is then held at this temperature for a set period of time, ensuring full homogenisation of the structure. The final critical step is rapid cooling in a suitably selected cooling medium, such as water, oil or compressed air, to obtain the hard martensitic structure responsible for the final properties of the steel.
Benefits of hardening:
- Increased hardness: the material becomes more resistant to plastic deformation and scratching.
- Improved durability: The ability of the material to carry loads without breaking is increased.
- Improved abrasion resistance: hardened parts wear more slowly under frictional conditions.
After hardening, a tempering process is often used to reduce the internal stresses and brittleness of the material, while maintaining high hardness. The use of specialised quenching furnaces and the appropriate expertise allows the quenching process to be carried out accurately for a wide range of steel grades.
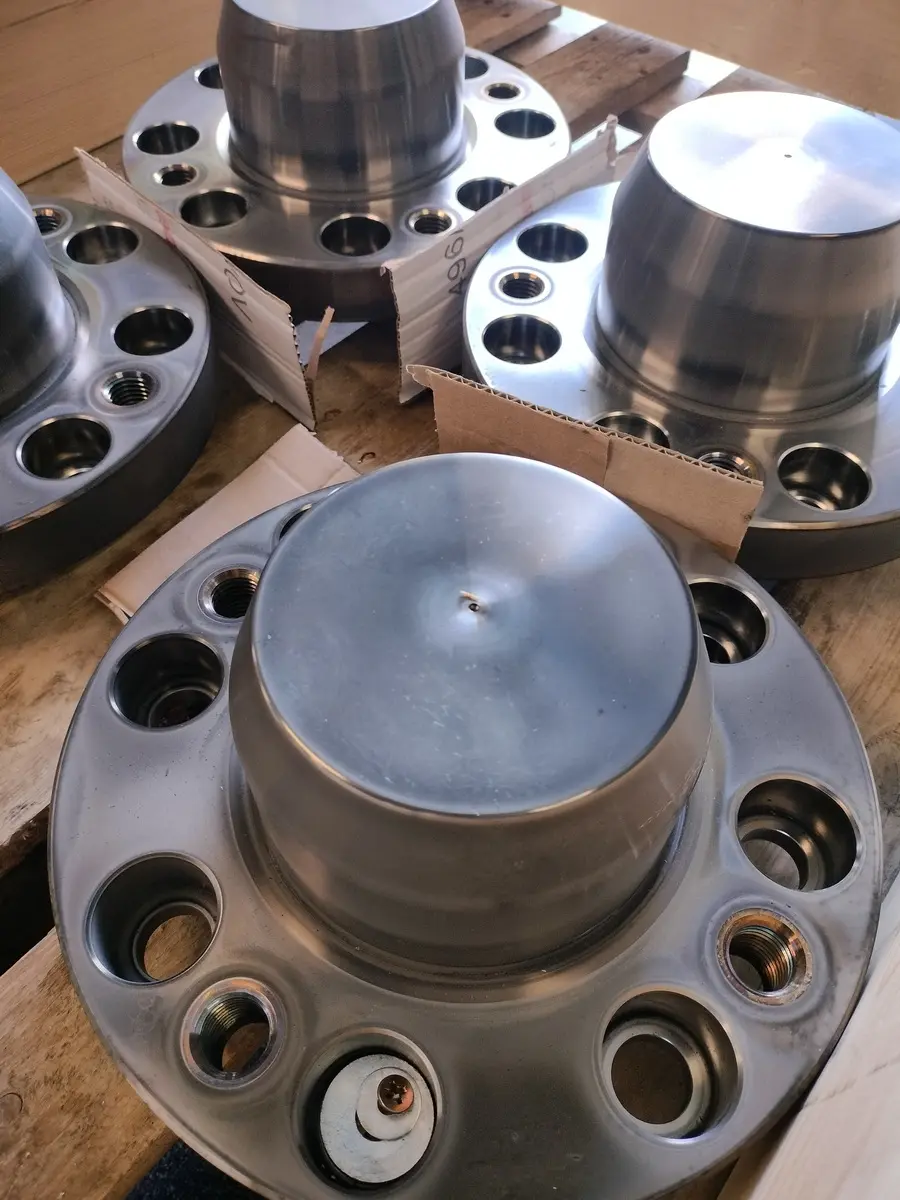
Nitration – Resistance to Abrasion and Corrosion
Nitriding is an advanced thermo-chemical treatment process that involves the diffusion saturation of the surface layer of steel objects with nitrogen atoms. During this process, carried out at elevated temperatures (usually in the range of 450-580°C), nitrogen atoms penetrate the structure of the steel, forming hard and stable nitrides with iron and other alloying elements present in the steel, such as chromium, molybdenum or aluminium. The result is a thin but extremely hard and wear-resistant nitrided layer, the thickness of which can vary from a few micrometres to about one millimetre, depending on the type of steel and the process parameters. This modified surface layer not only significantly increases resistance to mechanical wear, but also improves corrosion resistance by forming a barrier to aggressive agents, and increases the fatigue strength of components by introducing favourable compressive stresses. A significant advantage of nitriding is that it is carried out at temperatures lower than those used for hardening, which minimises the risk of deformation and dimensional changes in the workpieces, making it ideal for precision components.
Main advantages of nitriding:
- High surface hardness: Provides excellent resistance to abrasive wear.
- Increased corrosion resistance: Particularly for gas nitriding with controlled nitrogen potential.
- Improved fatigue strength: Components are more resistant to fracture under varying loads.
- Minimal deformation: Thanks to the low process temperature.
Various nitriding methods are available, including gas nitriding, which allows the composition of the atmosphere to be precisely controlled and optimum surface layer properties to be obtained. This service is particularly recommended for machine parts, tools and components subject to intensive wear.
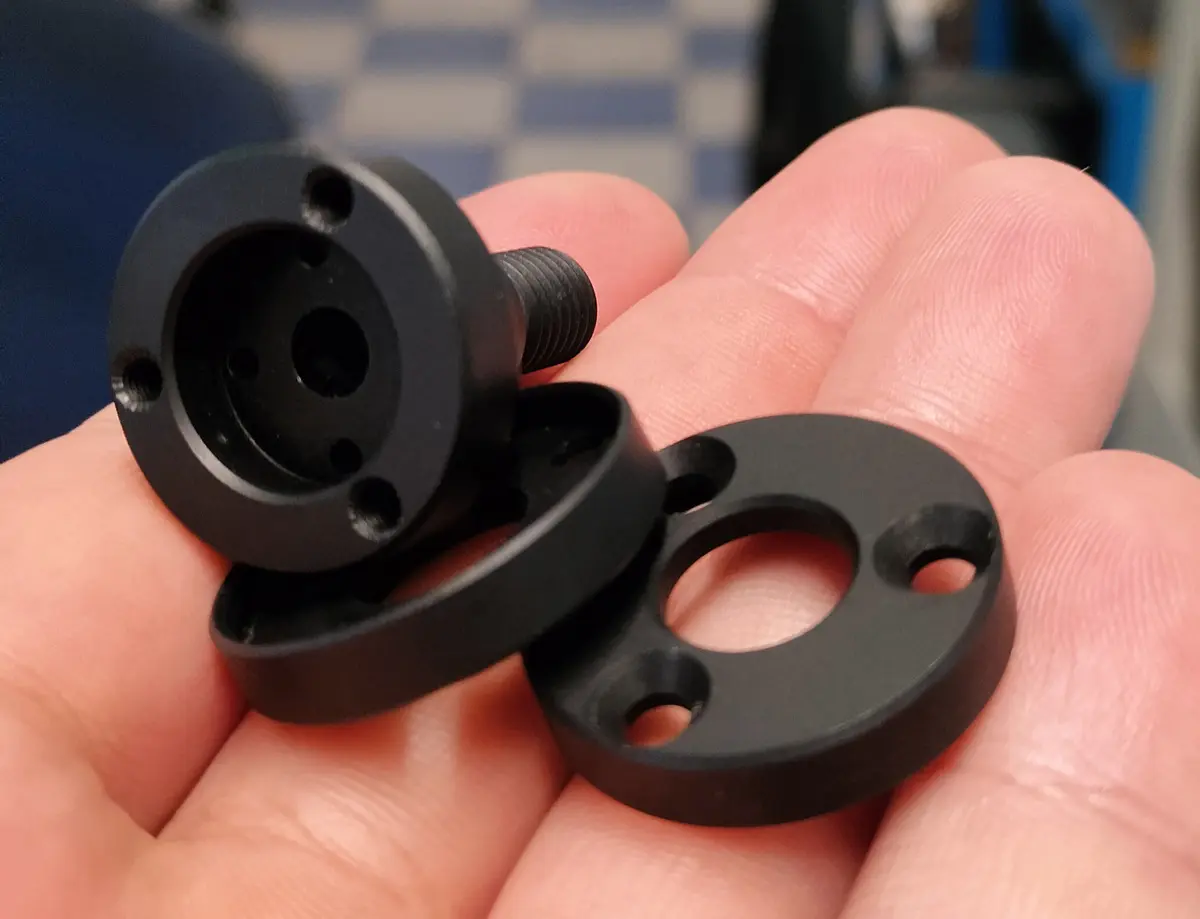
Anodising – Aluminium protection and aesthetics
Anodising, also known as anodisation, is an electrochemical process applied mainly to aluminium and its alloys. It involves the controlled formation of a durable, hard and non-metallic aluminium oxide (Al₂O₃) layer on the surface of the metal, which is integrally bonded to it. This carefully formed oxide layer significantly improves corrosion resistance, protects against degradation, increases abrasion resistance, and gives the surface an aesthetic, often coloured, appearance.
Key features of anodising:
- Corrosion protection: The oxide layer effectively insulates the aluminium from external influences.
- Increased hardness and abrasion resistance: The coating is harder than aluminium itself.
- Colourability: The anodic layer can be coloured in a variety of colours to enhance the aesthetics.
- Electrical insulation: Aluminium oxide is a good insulator.
At DWJ, the anodising process is carried out with attention to every detail, from surface preparation to the final sealing of the coating. As a result, customers receive products with excellent protective and decorative properties, which are used in construction, automotive, electronics or household goods manufacturing.
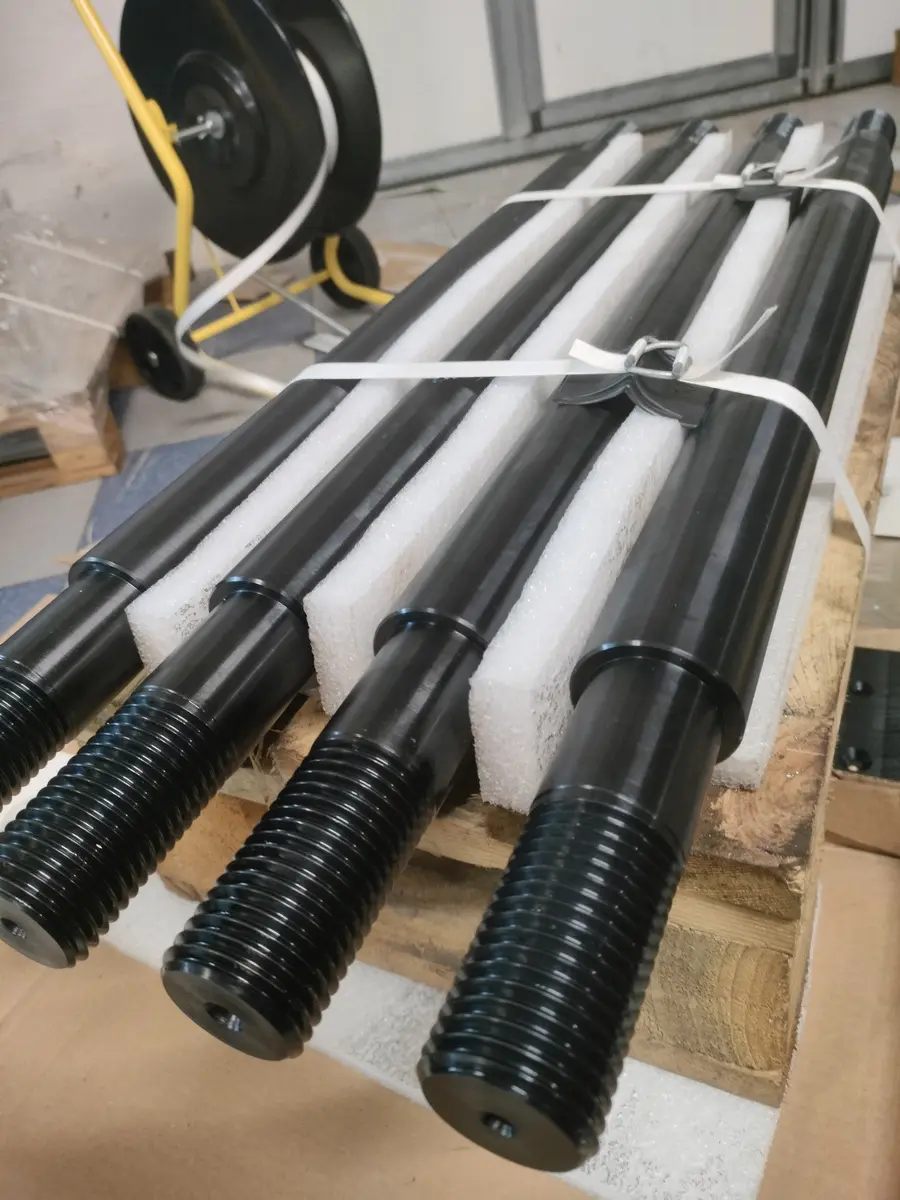
Blackening (Oxidation) – Protection and Appearance of Steel
Blackening, or oxidation, is a chemical process that produces a thin, conversion layer of iron oxides on the surface of steel, mainly stable magnetite (Fe₃O₄), which is an integral part of the metal. The main purpose of blackening is to improve corrosion resistance, which can be further enhanced by oiling, and to give components an aesthetically pleasing deep black finish. This process, often carried out by immersion, is relatively simple in technology and economical in application.
Advantages of blackening:
- Basic corrosion protection: Especially in combination with subsequent oiling.
- Aesthetic appearance: Gives steel an attractive black or dark grey colour.
- Minimal impact on dimensions: The thickness of the oxide layer is low.
- Improved adhesion for paints and lubricants.
Blackening services at DWJ are carried out using proven chemical baths, which guarantees even coverage and durability of the resulting coating. Blackening is often used for tools, machine parts, fasteners and firearms.
Summary
Specialised metalworking services such as x-hardening, nitriding, anodising and blackening play a key role in modern industry. They allow significant improvements in the performance and aesthetic properties of metal components, extending their life and increasing reliability. DWJ, thanks to its experience, advanced technological facilities and qualified staff, is able to meet the most demanding orders, providing services at the highest level. By choosing DWJ, customers invest in the quality and durability of their products.