Jak Wybrać Optymalne Parametry Obróbki CNC? Praktyczny Poradnik
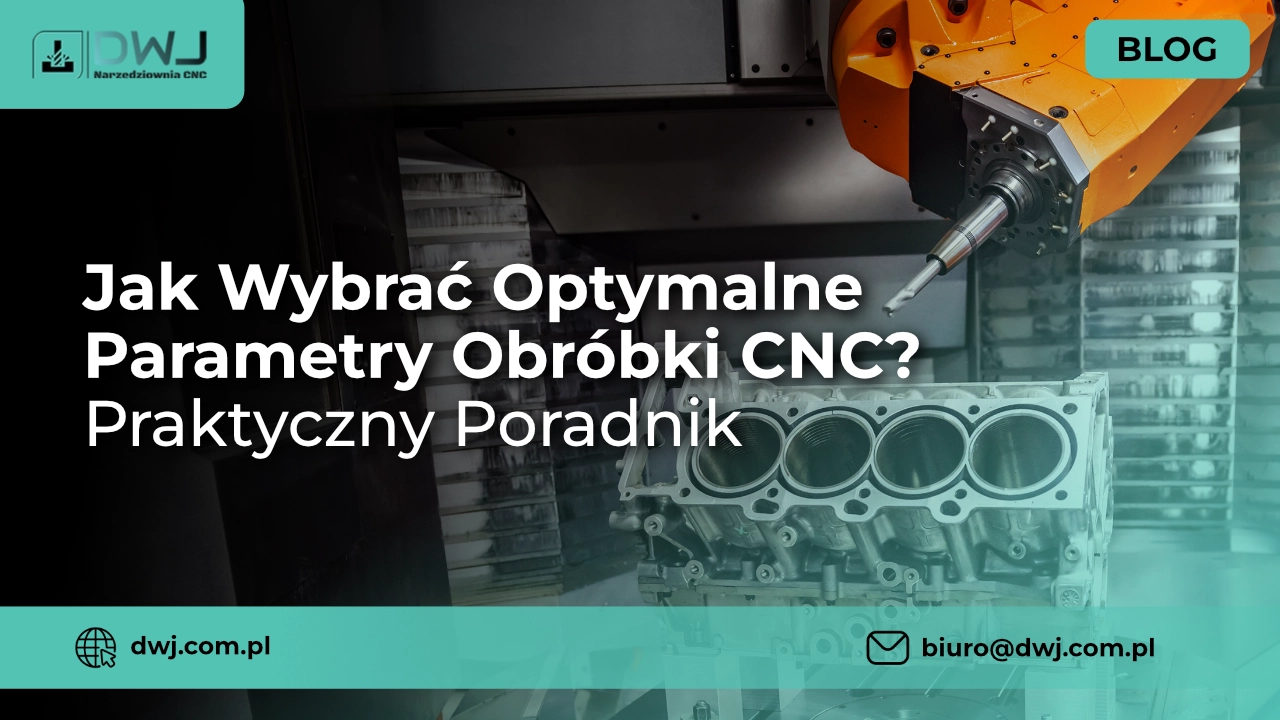
Obróbka CNC to proces, który wymaga precyzji, wiedzy i doświadczenia. Jednym z kluczowych czynników decydujących o jakości i efektywności tego procesu jest dobór optymalnych parametrów obróbki. Nieprawidłowe ustawienia mogą prowadzić do uszkodzenia narzędzi, obrabianego materiału, a nawet maszyny. W tym artykule przedstawimy praktyczny poradnik, jak wybrać najlepsze parametry obróbki CNC, aby osiągnąć doskonałe rezultaty.
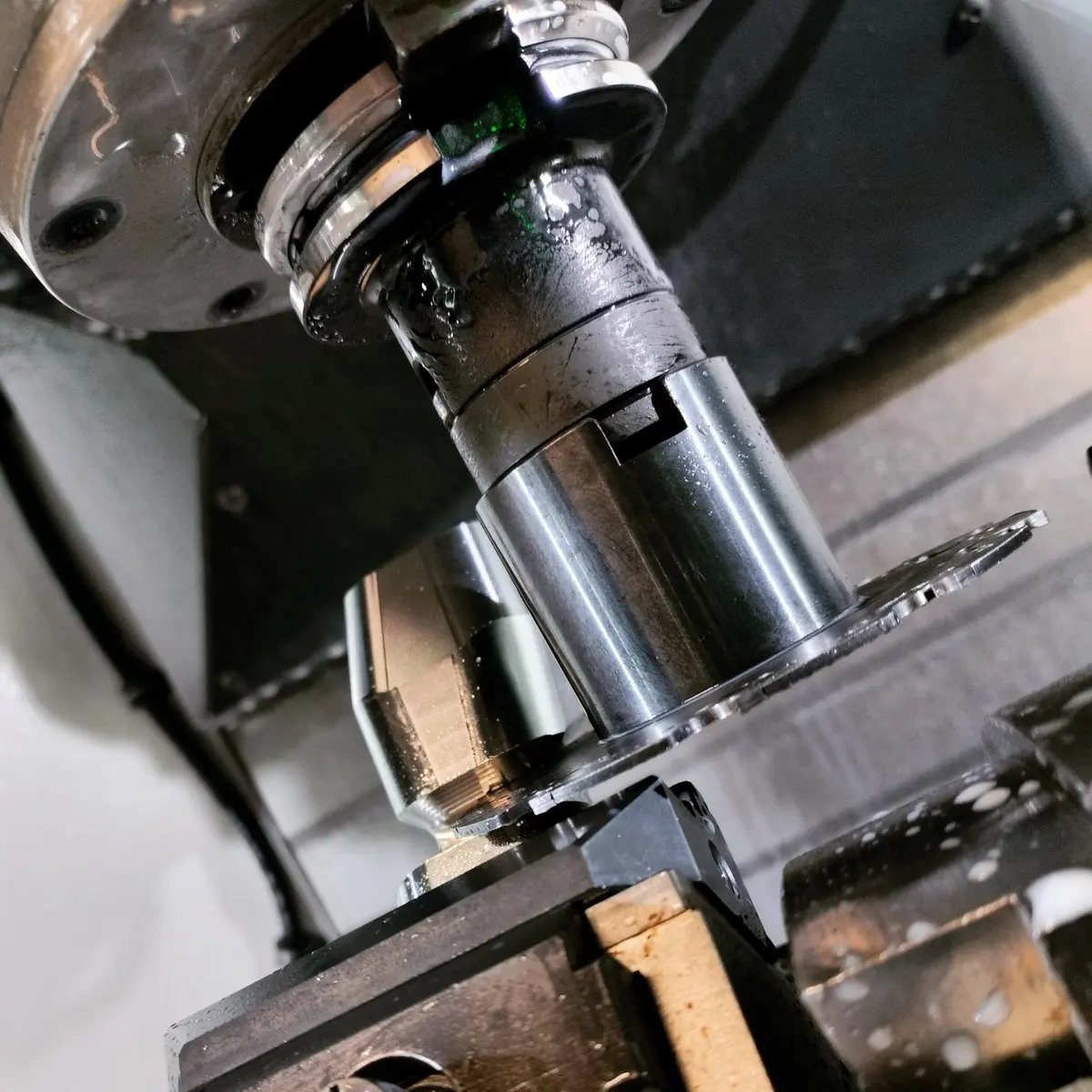
Zrozumienie Podstawowych Parametrów Obróbki CNC
Zanim przejdziemy do szczegółów, warto poznać podstawowe parametry, które wpływają na proces obróbki CNC:
Prędkość skrawania (Vc): Prędkość, z jaką krawędź skrawająca narzędzia porusza się względem materiału. Mierzona jest w metrach na minutę (m/min).
Prędkość obrotowa (n): Liczba obrotów wrzeciona na minutę (obr/min). Zależy od prędkości skrawania i średnicy narzędzia.
Posuw (f): Szybkość, z jaką narzędzie porusza się względem obrabianego materiału. Mierzony jest w milimetrach na obrót (mm/obr) lub milimetrach na minutę (mm/min).
Głębokość skrawania (ap): Głębokość, na jaką narzędzie wchodzi w materiał podczas jednego przejścia. Mierzona jest w milimetrach (mm).
Wybór Prędkości Skrawania (Vc)
Prędkość skrawania jest jednym z najważniejszych parametrów, ponieważ wpływa na żywotność narzędzia, jakość powierzchni i wydajność procesu. Zbyt wysoka prędkość może prowadzić do przegrzania narzędzia, a zbyt niska – do nieefektywnej obróbki.
Jak dobrać prędkość skrawania?
- Materiał obrabiany: Każdy materiał ma zalecaną prędkość skrawania przez producenta płytek skrawających, których używamy. Każdy producent narzędzi określa prędkość minimalną, maksymalną oraz wyjściową dla danego narzędzia. Warto patrzeć na opakowania płytek lub katalog narzędziowy.
- Rodzaj narzędzia: Głównie używane narzędzia to płytki i frezy z węglika spiekanego, ceramika, CBN. Kiedyś często stosowano HSS, gdzie prędkości skrawania były niskie.
- Warunki obróbki: Chłodzenie, stabilność mocowania, maszyna i rodzaj obróbki (np. zgrubna czy wykańczająca) również wpływają na wybór prędkości.
Dobór Prędkości Obrotowej (n)
Prędkość obrotowa jest bezpośrednio związana z prędkością skrawania i średnicą narzędzia. Można ją obliczyć za pomocą wzoru:
n=Vc×1000π×Dn=π×DVc×1000
gdzie:
- nn – prędkość obrotowa (obr/min),
- Vc – prędkość skrawania (m/min),
- DD – średnica narzędzia (mm).
Przykład:
Jeśli prędkość skrawania wynosi 250 m/min, a średnica frezu to 10 mm, prędkość obrotowa będzie wynosić:
n=250×10003.14×10≈7962 obr/minn=3.14×10250×1000≈7962obr/min
Ustalenie Posuwu (f)
Posuw decyduje o tym, jak szybko narzędzie porusza się względem materiału. Zbyt wysoki posuw może prowadzić do uszkodzenia narzędzia, a zbyt niski – do wydłużenia czasu obróbki i szybszego ścierania się krawędzi skrawającej.
Jak dobrać posuw?
- Zbyt niski: może prowadzić to szybszego stępienia narzędzia, może powstawać narost i jest mniej ekonomiczny. Głownie stosowany do obróbki wykończeniowej.
- Zbyt wysoki: może prowadzić do wykruszenia się krawędzi skrawającej, może występuje wysoka chropowatość powierzchni i odkształcenie materiału.
Głębokość Skrawania (ap)
W toczeniu ap określa promieniową grubość warstwy materiału usuwaną w jednym przejściu noża tokarskiego.
- Toczenie zgrubne (duża objętość skrawanego materiału)
ap = 1–10 mm (czasem więcej w przypadku maszyn o dużej sztywności), większa głębokość pozwala na szybsze usuwanie materiału, ale wymaga mocnej obrabiarki, stosowane przy obróbce surowych odlewów, wałów, rur.
- Toczenie wykańczające (precyzyjna obróbka, lepsza jakość powierzchni)
ap = 0,05–2 mm, mała głębokość pozwala osiągnąć gładką powierzchnię, wymaga ostrych narzędzi i małej prędkości posuwu.
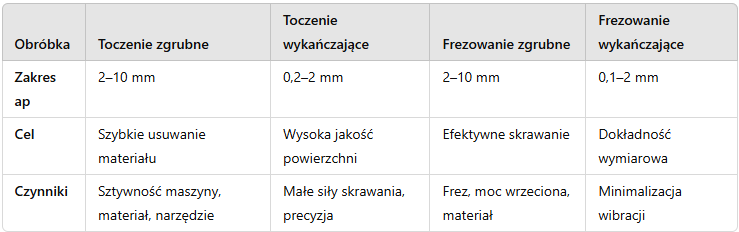
Czynniki wpływające na ap w toczeniu:
Materiał obrabiany – dla stali ap ≈ 2-6 mm, dla aluminium można stosować większe wartości. Sztywność układu tokarskiego – wibracje ograniczają maksymalne ap. Rodzaj noża tokarskiego – noże z płytkami węglikowymi pozwalają na większe ap.
W frezowaniu ap oznacza różnicę wysokości między powierzchnią obrabianą a najniższym punktem skrawania freza.
Jak dobrać ap w frezowaniu?
- Frezowanie zgrubne (szybkie usuwanie materiału)
ap = 2–10 mm (w zależności od sztywności obrabiarki), można stosować większą głębokość przy frezowaniu walcowo-czołowym i dużych frezach.
- Frezowanie wykańczające (precyzyjna obróbka, lepsza jakość powierzchni)
ap = 0,1–2 mm, mała głębokość zapewnia wysoką dokładność wymiarową.
Czynniki wpływające na ap w frezowaniu
- Rodzaj freza – większe średnice freza pozwalają na większą ap.
- Sztywność wrzeciona i oprawki – ogranicza maksymalną głębokość skrawania.
- Rodzaj frezowania – frezowanie czołowe → większa ap, frezowanie obwodowe→ ap zależy od szerokości freza.
- Moc obrabiarki – większa ap wymaga mocniejszego wrzeciona.
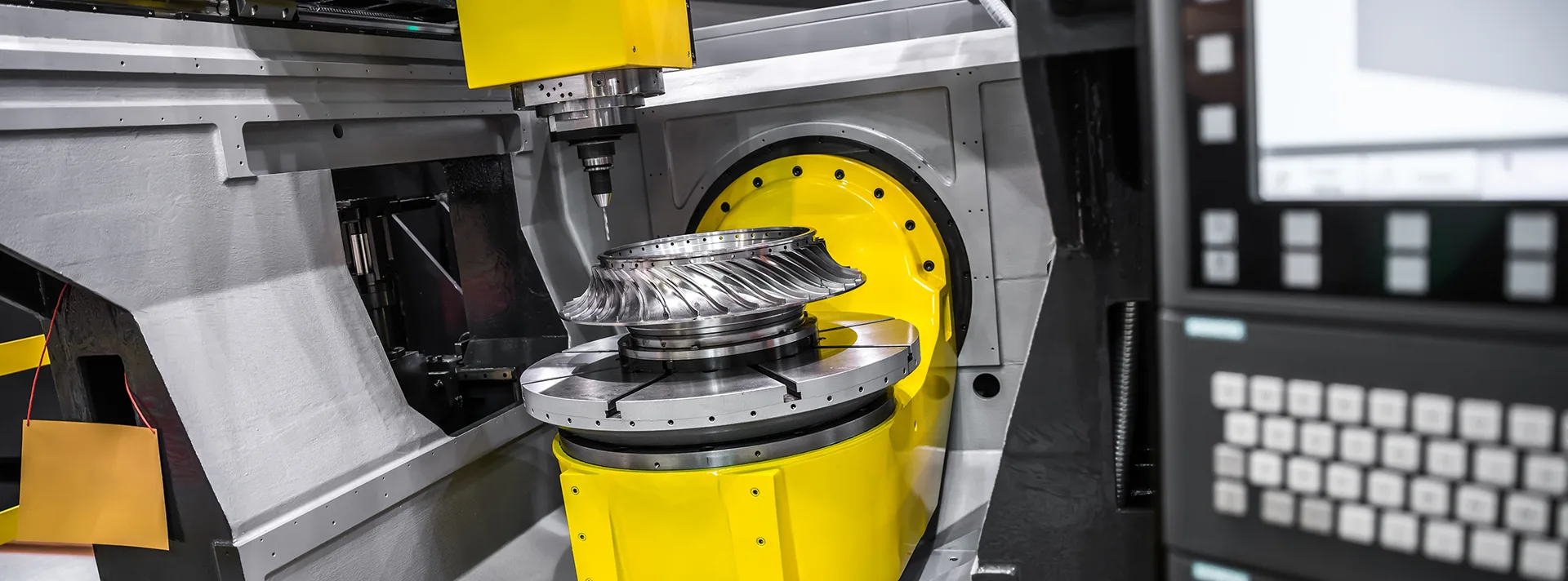
Uwzględnienie Chłodzenia i Smarowania
Odpowiednie chłodzenie i smarowanie są kluczowe dla wydłużenia żywotności narzędzia i poprawy jakości obróbki. W zależności od materiału i rodzaju obróbki można stosować:
- Chłodzenie cieczą:
– Toczenie i frezowanie stali, aluminium i stopów żeliwa.
– Obróbka wymagająca dużych prędkości skrawania i precyzji.
– Głębokie wiercenie, gdzie odprowadzanie wiórów jest kluczowe
- Chłodzenie powietrzem:
– Obróbka aluminium, stopów magnezu i kompozytów.
– Operacje, w których chłodziwo mogłoby zanieczyścić materiał lub powodować szok termiczny dla krawędzi skrawającej.
– Frezowanie cienkościennych elementów, gdzie chłodziwo mogłoby powodować odkształcenia.
- Obróbka na sucho:
– Twarde toczenie z użyciem narzędzi ceramicznych lub CBN.
– Materiały wrażliwe na ciecze chłodzące (np. niektóre kompozyty).
– Obróbka sucha w przemyśle lotniczym i motoryzacyjnym.
Testowanie i Optymalizacja
Dobór parametrów obróbki CNC to proces iteracyjny. Zaleca się:
- Testowanie na próbkach: Przetestuj różne parametry na małych fragmentach materiału bądź na próbnej partii.
- Monitorowanie procesu: Obserwuj zużycie narzędzia, jakość powierzchni i czas obróbki.
- Korekta parametrów: Dostosuj parametry na podstawie wyników testów.
Podsumowanie
Wybór optymalnych parametrów obróbki CNC to klucz do efektywnej i precyzyjnej produkcji. Pamiętaj, że każdy materiał, narzędzie i projekt wymaga indywidualnego podejścia. Korzystając z powyższych wskazówek, możesz znacząco poprawić jakość obróbki, wydłużyć żywotność narzędzi i zwiększyć wydajność procesu. Jeśli masz wątpliwości, zawsze warto skonsultować się z doświadczonym operatorem CNC lub inżynierem.